Upcoming Sessions
- There are no upcoming sessions scheduled
See All Upcoming Sessions
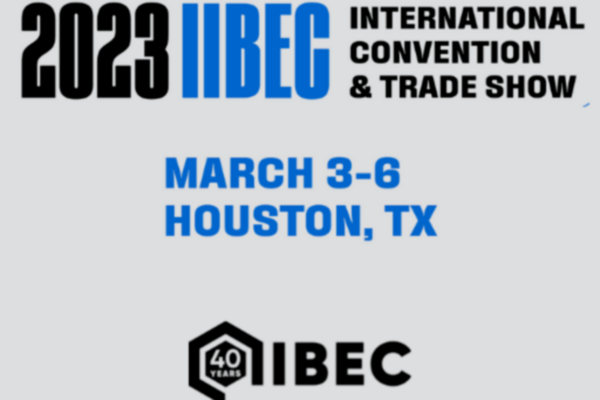
These 5 sessions were originally presented at the 2023 IIBEC International Convention & Trade Show in Houston, Texas. The courses include the recording of the session, a summative assessment consisting of 10 multiple-choice questions, and surveys required to claim continuing education credit. The bundle includes the following courses: Assessment of Thermal Bridging of Fasteners through Insulated Roof Assemblies Oh Hail! Metal Roofs, Hail Impact, and Long-Term Performance Wind Tunnel Testing of Edge Metal Resilience and the Impact on Roofing Lightning Protection Systems: Coordinating with the Building Enclosure Read more
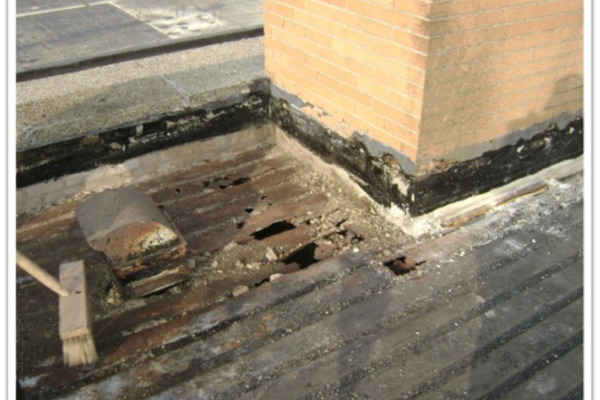
Rooftop Quality Assurance Course Description Rooftop Quality Assurance (RTQA) is an 8-hour course for professionals interested in performing observation services to ensure the roof installation is consistent with construction documents and ownership requirements. The program includes thorough overviews of the major roof system assemblies which the professional observer will encounter when performing rooftop quality assurance services for ownership/design groups. The course includes in-depth descriptions of the observer’s roles and responsibilities for proven success in the field. RTQA is designed to cover all aspects of the rooftop quality assurance process, including differing roof installation conditions, and resolving issues that arise during construction and renovation. The course is ideal for roofing material manufacturers, general contractors, quality assurance observers, architectural and engineering field techs, and field inspectors. Course Access Courses are accessible in LearnUpon for one year from the date of purchase. Credit Start Date: April 21, 2023 Credit Expiration Date: April 21, 2026 Course Prerequisites None Knowledge Level: Intermediate Continuing Education Credit Statement This course is approved for 8.0 IIBEC CEH This course is approved for 8.0 AIA LU HSW Continuing Education Credit Claim Information In order to claim IIBEC CEHs, learners are required to: Achieve a passing score of 70% on the summative assessment (learners are provided unlimited attempts) Complete the course Evaluation & Attestation Survey After completing the Evaluation & Attestation Survey, learners will be able to download a Certificate of Completion. Learners are responsible for self-reporting IIBEC CEH credit by uploading their Certificate of Completion to their IIBEC Portal. For assistance in self-reporting CEHs, please reach out to: [email protected] In order to claim AIA LU, learners are required to complete the above requirements, as well as: Complete the AIA Survey (AIA member number is required) AIA continuing education Learning Units earned upon completion of this course will be reported to AIA CES for AIA members. Course Author(s)/Reviewer(s) Jerry Abendroth, RRC, RBEC, CDT Burt Carver, RRC, RRO Jon Peat, RRC, RRO Michel Paulin Course Presenter(s) Jerry Abendroth, RRC, RBEC, CDT Burt Carver, RRC, RRO AIA Course Number : RTQA- OD12.22 AIA CES Provider statement IIBEC is a registered provider of AIA-approved continuing education under Provider Number G024. All registered AIA CES Providers must comply with the AIA Standards for Continuing Education Programs. Any questions or concerns about this provider or this learning program may be sent to AIA CES ([email protected] or (800) AIA 3837, Option 3). This learning program is registered with AIA CES for continuing professional education. As such, it does not include content that may be deemed or construed to be an approval or endorsement by the AIA of any material of construction or any method or manner of handling, using, distributing, or dealing in any material or product. AIA continuing education credit has been reviewed and approved by AIA CES. Learners must complete the entire learning program to receive continuing education credit. AIA continuing education Learning Units earned upon completion of this course will be reported to AIA CES for AIA members. Certificates of Completion for AIA members are available upon request. Read more
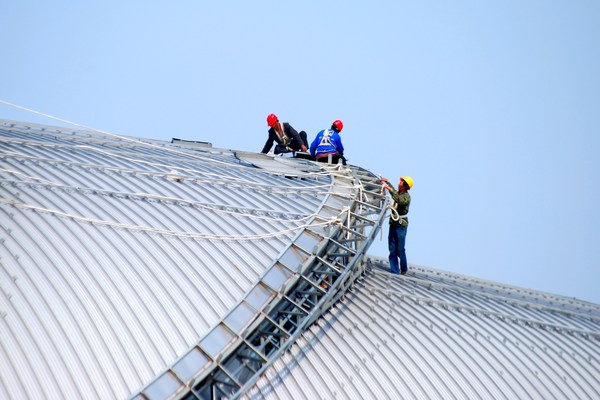
This 8-hour course is structured for those who have already passed the RRC exam and want a review of skills and to be updated with new information, and those who have the necessary tools to complete the RRC registration exam and desire a quick brush-up on technical topics as a review. Covered during the program: wind design, including ASCE 7 and FM Global requirements; thermal calculations; CSI changes; green-roofing principles; and roof asset management (RAM) calculations. Updated information is provided in all areas. 8 IIBEC Continuing Educational Hours Emily Lorenz, Sr. Director of Technical Services, IIBEC Brian Gardiner, Director of Industry Affairs, IIBEC Warren French, President, French Engineering, LLC Jerry Abendroth, Senior Consultant, Intertek PSI Ray Wetherholt, Wetherholt and Associates, Inc. Read more
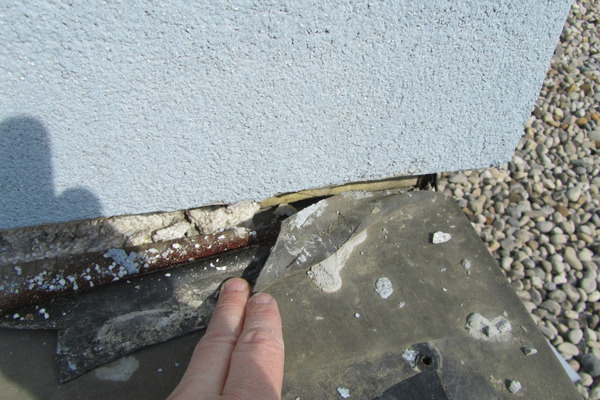
This course was initially presented at the 2021 International Convention and Tradeshow. Water-related damage is common at parapet terminations with high-rising walls that lack proper integration of the four primary control layers. The speaker has found that except for EIFS manufacturers’ standard details, there are little to no industry-recognized saddle flashing details available at this time to provide guidance to design professionals and contractors for the integration of the four primary control layers. Construction documents often do not include saddle flashing details or specification requirements, and consideration needs to be given to construction sequencing when developing the details. Due to the lack of industry-recognized details, a set of multi-step isometric details was developed by Michael Nagle, showing the integration of the air/weather-resistive barriers, roofing membrane, through-wall flashing, and sheet metal flashing for inclusion in one or more industry-recognized detail manuals. He recently collaborated with the International Masonry Institute (IMI) to construct saddle flashing mock-ups with the assistance of a manufacturer and multiple contractors. The mock-ups will be used as educational tools for masons, roofers, and design professionals. This presentation will provide beneficial guidance to building enclosure consultants, design professionals, building owners, facility managers, and manufacturers. Michael Nagle, RA, NCARB Wiss, Janney, Elstner Associates | Cleveland, OH Michael Nagle is a building enclosure consultant with specializations in façade, windows, and roofing problems in existing, historic, and new buildings. Since joining WJE in 2004, he has provided professional services for numerous projects involving water and air infiltration, condensation, and distress conditions in a variety of building enclosure systems, including brick masonry, stone, terra cotta, windows, curtainwall, metal wall panels, EIFS, stucco, sealants, roofing, and waterproofing. He is an active member in the Cleveland chapter of the Building Enclosure Council and chair of the ASTM C24.10 Building Seals and Sealants Subcommittee. Read more
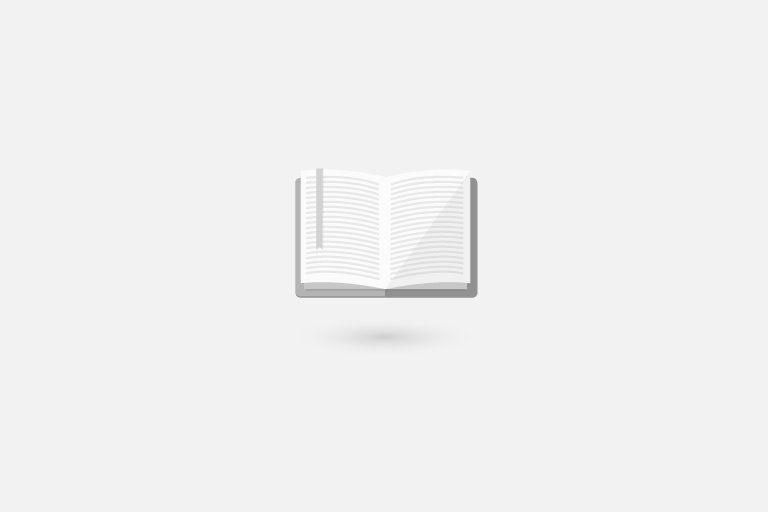
In the architecture, engineering, and construction (AEC) industry, several disciplines have seen how small unmanned aircraft systems (sUAS) or drones can make critical, and sometimes dangerous, tasks more efficient, precise, and accessible. This includes using drones to perform thermal imaging scans to detect air, moisture, and heat leakage from a building enclosure—the glass, concrete, insulation, and other materials separating the inside and outside environments. Leaky buildings can be costly and dangerous, leading to damaged finishes, increased energy costs, and mold growth within walls and roofs. Infrared thermography is a relatively cost-effective, easy-to-use, non-destructive tool for these types of conditions, but requires expert interpretation. SGH has implemented the use of drones on many projects, and by using drone technology, AEC professionals can get detailed results to make informed recommendations that address underlying building concerns. In this paper/presentation, we will explore how the AEC industry has implemented drone use to conduct thermal imaging scans of buildings, discuss some of the nuances with using drones around building enclosures, and discuss the differences compared to handheld scanning techniques. We will review industry standards and guidelines and share common project challenges and opportunities through a series of case studies. Kelsey Dunn, PE Simpson Gumpertz & Heger | Boston, MA Kelsey A. Dunn joined SGH in September of 2013 and is a senior staff engineer in SGH’s building technology group in Boston, MA. Dunn has been involved in a variety of projects involving investigation, design, and construction administration for existing building repair projects, rehabilitation of historic buildings, and new construction building-enclosure consulting. She has performed many partial and whole-building infrared scans using both the handheld and sUAS/drones while at SGH. Christopher Grey, PE Simpson Gumpertz & Heger | Boston, MA Christopher N. Grey joined SGH in 2011 and is a senior project manager in SGH’s building technology group in Boston, MA. His experience includes investigating, rehabilitating, and designing building enclosure systems on a wide range of project types, from historic buildings to contemporary high-rise structures. He specializes in the design, integration, construction administration, and in-situ testing of complex building enclosure systems with a focus on design efficiency, constructability, and performance. He works directly with architects, owners, contractors, and manufacturers in both the field and office through all project phases. Grey has performed many partial- and whole-building infrared scans, assists with managing SGH’s internal sUAS/drone usage and standards, is a certified sUAS Level I Thermographer, and also a contributing member of the American Architectural Manufacturer’s Association, serving on several industry standard task groups. Read more
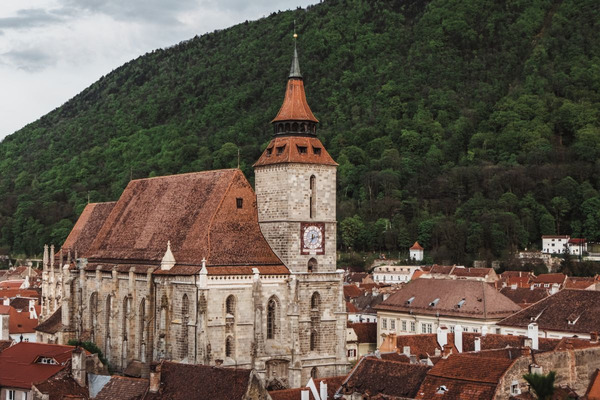
This presentation was initially provided at the 2021 Convention and Tradeshow in Phoenix, Arizona Do you get projects that may involve steep roofs? The Roofing Industry Committee on Weather Issues (RICOWI) has inspected hundreds of steep roofs as part of its Wind Investigation Program (WIP). These post-hurricane investigations have led to a better understanding of the strengths and weaknesses of the wind performance of metal panel, tile, and asphalt shingle roofs. This presentation will discuss the systems, strengths, and detail where consultants and inspectors can focus to ensure a wind-resistant steep roof. Since the inception of the RICOWI WIP in 1996, there has been wind tunnel, full-scale and laboratory-designed wind research and testing. This research has resulted in better products and systems, but the fury and duration of hurricanes test every aspect of design and installation. Using photos from six WIP investigations, participants will see how systems have improved and where more attention is needed. This information can be used to design roofs for all climates and wind zones. David Roodvoets DLR Consultants | Tampa, FL David Roodvoets has had a leadership role in all six RICOWI hurricane investigations. He has worked with ARMA on asphalt shingle wind resistance and test standards and has been involved with post-storm wind damage investigations for 40 years. Roodvoets has worked with wind research engineers in testing of asphalt shingles, vegetative systems, photovoltaic systems, single-ply, and ballasted roof systems. As a result, manufacturers have incorporated improved design and installation requirements, and changes have been developed, advocated for, and incorporated into the ICC family of codes. Read more
Shopping Cart
Your cart is empty