Upcoming Sessions
- There are no upcoming sessions scheduled
See All Upcoming Sessions
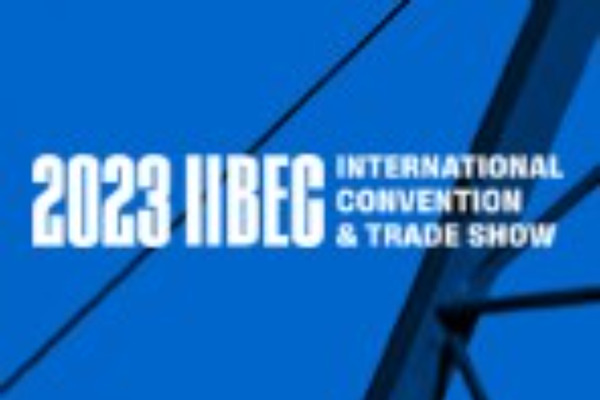
Course Overview This session was originally presented at the 2023 IIBEC International Convention & Trade Show in Houston, Texas. This course includes the recording of the session, a summative assessment consisting of 10 multiple-choice questions, and surveys required to claim continuing education credit. Description Exterior wall assemblies serve many functions. Architects must design buildings that are energy efficient, manage bulk water, and reduce air leakage in addition to meeting the fire performance standards required by the International Building Code (IBC). It is important to recognize that making changes to the exterior wall design may trigger the need to retest or reconsider all the wall functions. It is also important to understand that fire safety is not dependent upon the presence or absence of any one material or wall configuration. Performance testing such as NFPA 285 is a tool for gaining an understanding of how assemblies will perform. While fire containment and compartmentalization are often supported by performance testing, they are also part of a multilayered approach to fire safety that must include prevention, detection, occupant protection, and extinguishment. Course Start Date February 22, 2023 Course Expiration Date February 22, 2026 Course Prerequisites None Knowledge Level: Intermediate Continuing Education Credit Statement This course is approved for 1.0 IIBEC CEH. This course is approved for 1.0 AIA LU HSW. Continuing Education Credit Claim Information In order to claim IIBEC CEHs, learners are required to: Achieve a passing score of 100% on the summative assessment (learners are provided unlimited attempts) Complete the course Evaluation & Attestation Survey After completing the Evaluation & Attestation Survey, learners will be able to download a Certificate of Completion. Learners are responsible for self-reporting IIBEC CEH credit by uploading their Certificate of Completion to their IIBEC Portal. For assistance in self-reporting CEHs, please reach out to: [email protected] In order to claim AIA LU, learners are required to complete the above requirements, as well as: Complete the AIA Survey (AIA member number is required) AIA continuing education Learning Units earned upon completion of this course will be reported to AIA CES for AIA members. Author(s)/Speaker(s) Eric Banks E.W. Banks Consulting LLC | Houston, TX Justin Koscher Polyisocyanurate Insulation Manufacturers Association | Mount Pleasant, SC AIA Course Number: 06.23ConOD AIA CES Provider statement IIBEC is a registered provider of AIA-approved continuing education under Provider Number G024. All registered AIA CES Providers must comply with the AIA Standards for Continuing Education Programs. Any questions or concerns about this provider or this learning program may be sent to AIA CES ([email protected] or (800) AIA 3837, Option 3). This learning program is registered with AIA CES for continuing professional education. As such, it does not include content that may be deemed or construed to be an approval or endorsement by the AIA of any material of construction or any method or manner of handling, using, distributing, or dealing in any material or product. AIA continuing education credit has been reviewed and approved by AIA CES. Learners must complete the entire learning program to receive continuing education credit. AIA continuing education Learning Units earned upon completion of this course will be reported to AIA CES for AIA members. Certificates of Completion for AIA members are available upon request. Read more
Course Overview This session was originally presented at the 2023 IIBEC International Convention & Trade Show in Houston, Texas. This course includes the recording of the session, a summative assessment consisting of 10 multiple-choice questions, and surveys required to claim continuing education credit. Description The deeper the foundation, the higher the risk for water infiltration. Below-grade waterproofing systems are a critical part of the overall building enclosure and should be carefully selected to properly protect the structure and interior below-grade space. This presentation will discuss the challenges specific to deep foundation waterproofing as well as provide best practices for various below-grade elements with which the waterproofing will interface. New construction project examples and scenarios will be included to elaborate on the challenges, discussions, and solutions.. Credit Start Date February 16, 2023 Credit Expiration Date February 16, 2026 Course Prerequisites None Knowledge Level: Intermediate Continuing Education Credit Statement This course is approved for 1.0 IIBEC CEH. This course is approved for 1.0 AIA LU HSW. Continuing Education Credit Claim Information In order to claim IIBEC CEHs, learners are required to: Achieve a passing score of 100% on the summative assessment (learners are provided unlimited attempts) Complete the course Evaluation & Attestation Survey After completing the Evaluation & Attestation Survey, learners will be able to download a Certificate of Completion. Learners are responsible for self-reporting IIBEC CEH credit by uploading their Certificate of Completion to their IIBEC Portal. For assistance in self-reporting CEHs, please reach out to: [email protected] In order to claim AIA LU, learners are required to complete the above requirements, as well as: Complete the AIA Survey (AIA member number is required) AIA continuing education Learning Units earned upon completion of this course will be reported to AIA CES for AIA members. Author(s)/Speaker(s) Amos Chan, PE, BECxP, CxA+BE Walter P Moore & Associates |Atlanta, GA AIA Course Number: 03.23ConOD AIA CES Provider statement IIBEC is a registered provider of AIA-approved continuing education under Provider Number G024. All registered AIA CES Providers must comply with the AIA Standards for Continuing Education Programs. Any questions or concerns about this provider or this learning program may be sent to AIA CES ([email protected] or (800) AIA 3837, Option 3). This learning program is registered with AIA CES for continuing professional education. As such, it does not include content that may be deemed or construed to be an approval or endorsement by the AIA of any material of construction or any method or manner of handling, using, distributing, or dealing in any material or product. AIA continuing education credit has been reviewed and approved by AIA CES. Learners must complete the entire learning program to receive continuing education credit. AIA continuing education Learning Units earned upon completion of this course will be reported to AIA CES for AIA members. Certificates of Completion for AIA members are available upon request. Read more
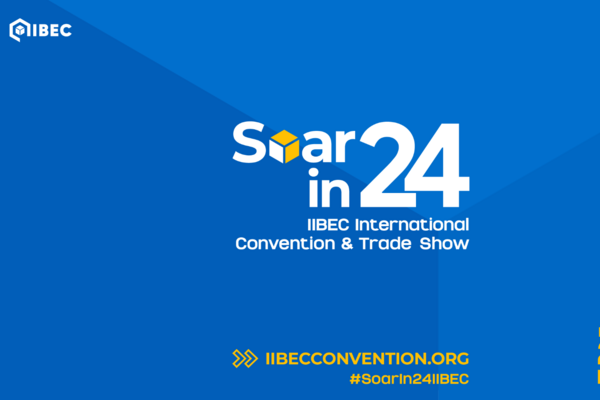
This bundle includes 4 sessions from the 2024 IIBEC Convention focusing on restoration and repairs. Each session in this bundle qualifies for 1.0 IIBEC CEH and 1.0 AIA LU/HSW. - The Current State of Embodied Carbon and Building Enclosures - Avoiding Pitfalls with Large Skylight Design and Maintenance - Simplifying Whole Building Airtightness - Trust the Process: The Nuances of BECx Read more
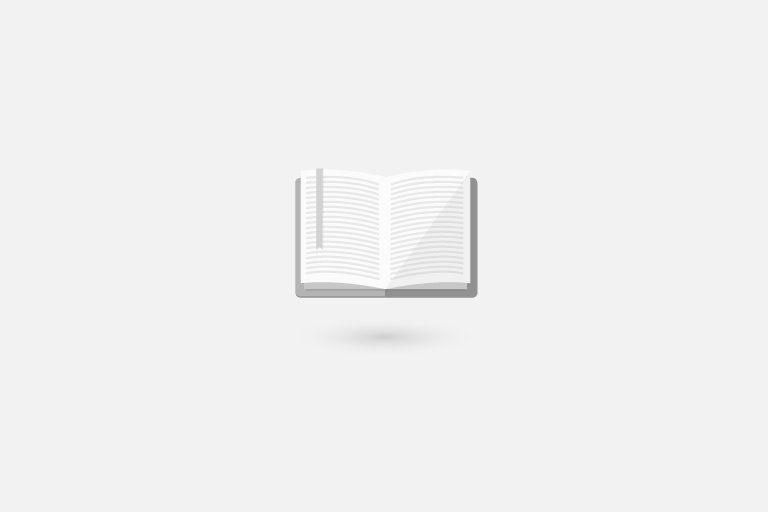
This bundle includes 5 sessions from the 2024 IIBEC Convention focusing on restoration and repairs. Each session in this bundle qualifies for 1.0 IIBEC CEH and 1.0 AIA LU/HSW. Read more
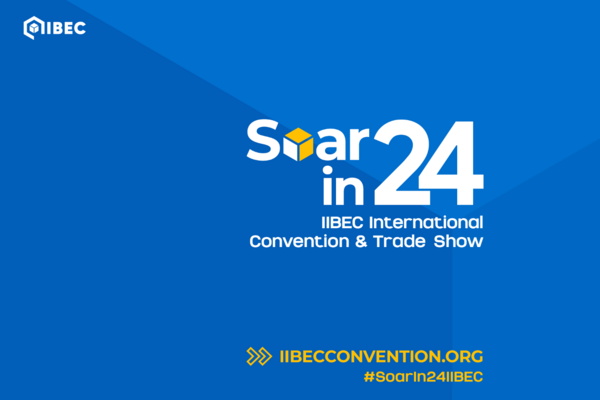
This bundle includes 6 sessions from the 2024 IIBEC Convention focusing on restoration and repairs. Each session in this bundle qualifies for 1 IIBEC CEH and/or 1.AIA LU or 1.AIA LU /HSW. Bundle includes the following presentations: - Restoration of Historic Temple Emanu-El - Mass Timber Moisture Protection - Hygrothermal Efficiency of Retrofit Wall Cladding System for Existing Buildings - Integrated Enclosure Detailing at the BIDMC New Inpatient Building - Glass Distortion: Not Such a Clear View - Condo Chronicles: Navigating Condominium Fenestration Replacement and Restoration Projects Read more
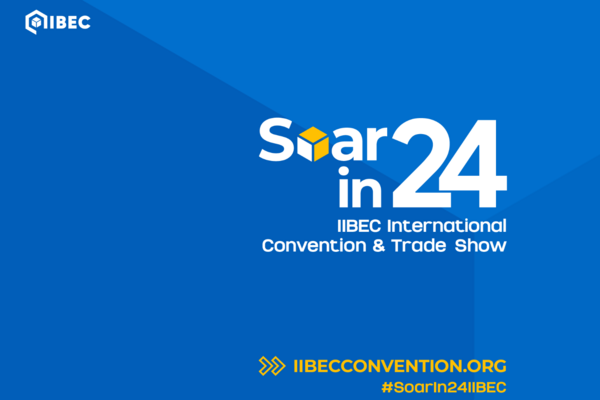
This bundles includes 5 sessions from the 2024 IIBEC Convention focusing on restoration and repairs. Each session in this bundle qualifies for 1.0 IIBEC CEH and 1.0 AIA LU/HSW. Read more
Shopping Cart
Your cart is empty